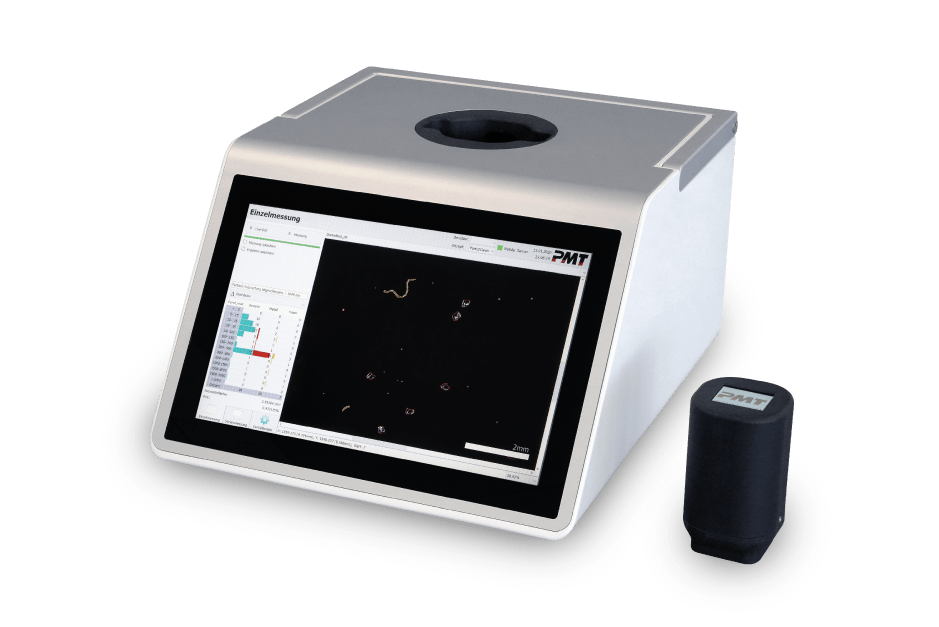
On-site Surface Particle MonitorPartSens
Measures numbers and sizes
of deposited particles in 10 seconds.
- ISO14644-9
- ISO14644-13
- VDA19.2
Measures numbers and sizes
of deposited particles in 10 seconds.
Particles size of 5µm or more called "macroparticles" are difficult to measure with an air particle counter as they fall and deposit in a cleanroom. These uncontrolled particles fall and deposit on the surfaces of manufacturing systems, contaminating the manufacturing environment. Furthermore, these particles redisperse in the air and be transported with physical contacts by people and the systems. Once these macroparticles are deposited, it is difficult to control the contamination. An appropriate cleaning program must be established and effective cleaning must be performed to solve the contamination problems.
PartSens is a portable surface monitor that instantly measures the size and number of macroparticles on any surface of a cleanroom manufacturing environment. PartSens classifies the particles into reflective, non-reflective, and fiber. It evaluates various applications related to surface cleanliness such as cleaning efficiency of pre-cleanroom, air showers, floors, walls, equipment, clothes, gloves, and products.
Measuring principle | Glancing light technology (in accordance with ISO14644-9) |
---|---|
Detectable items | Particle sizes , numbers , classifications (particles and fibers) |
Detection range(Feret-max) | Non-metallic particles 2µm - >3000µm Metallic particles 25µm - >3000µm Fibers 50µm - >3000µm |
Particle size allocation | According to VDA19.1 and ISO16232 |
Display types | Distributive, Distributive/1000 cm², Cumulative, Cumulative/1000 cm² |
Measuring time | <10 sec. |
Data storage capacity | 300 data |
Screen type | Touch screen, 12.1” TFT |
Languages | English, Japanese, German, French |
Screen resolution | 3872 × 2764 (pixels) |
Outputs | Network ( TCP/IP ) , USB Type A, HDMI |
Power supply | AC 100-240 V AC-1, 4 A 50/60 Hz | DC 24 VDC @ 5A Lithium-ion battery 2 × Nominal Voltage 11.1 V, 7800 mAh, 86, 58 W max. |
Weight | 7.7kg, 6.7kg |
Application temperature range | 5 - 30 ℃ ; 20 - 95% (RH) non-condensing |
Storage conditions | 0 - 50 ℃ ; up to 98% (RH) non-condensing |
Measuring area | 2.68cm2 (19.36 × 13.82mm) |
---|---|
Data transmission | WLAN 2.4 GHz |
Range of mobile measuring head | Operating range max. 10 meters away from the base unit |
Power supply | Lithium-ion battery |
Calibration | Once a year recommended |
Measuring device for tape lift pads | Included |
Screen type | Touch screen, LCD |
Traditionally, the use of airborne particle counters and microscopes were believed to be the best method for assessing a surface cleanliness level. However, these methods are not practical for monitoring macroparticles (≥5µm) because airborne particle counters can only detect particles that are small enough to keep floating in the air and can be vacummed by the particle counter, leaving all the macroparticles which falls onto surfaces undetected. Microscopes are not effective either, for they have a possibility of cross-contaminating samples. Cleanroom flashlights for visualizing contaminants also cannot detect macroparticles for cleanrooms required to control particles smaller than 100µm. PartSens is the only monitoring device to be listed in VDA 19.2 “Technical cleanliness in assembly” that replaces obsolete inspection methods, leading an innovative approach to prevent “transfer,” “contact,” and “deposition” of particles in a clean environment.
Depending on the mass and the air current, particles larger than ≥5-25µm eventually deposits and contaminate all surfaces. Particles on surfaces cannot be removed by Fan Filter Units, hence referred to as “unfiltered particles.” Walking, cleaning or any other activities cause these particles to be transferred to other areas of the facility or re-dispersed into the air, creating higher risks of contamination.