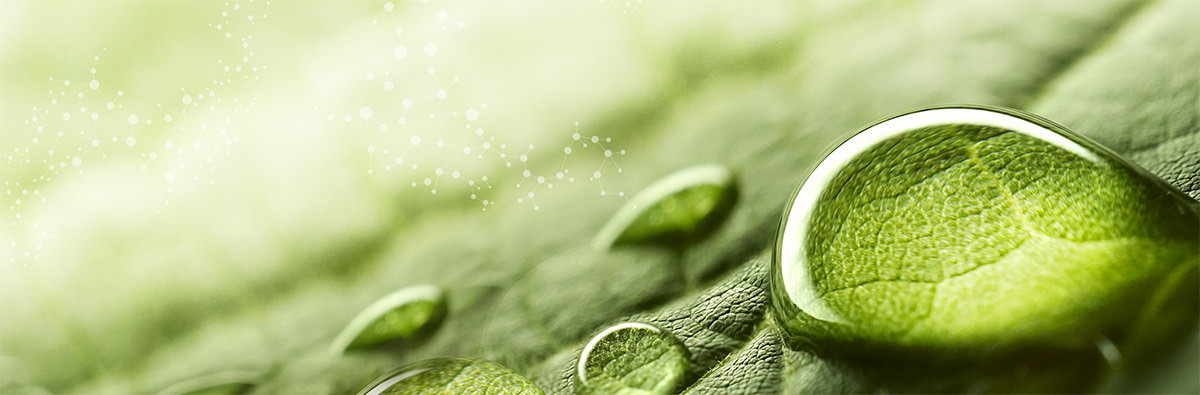
For all machinery that use oil and fuel, including automobiles, aircraft, construction machinery, and power generation need clean flushing fluid at the manufacturing stage and the shipping process in order to maintain their quality. Furthermore, the contaminants of several microns existing in fluid circuits wear and slide that cause malfunction for hydraulic equipment that requires complicated control at high pressure and lubrication system that requires long lasting expectancy. If cleanliness is not monitored and controlled proactively, it will lead to machine failure.
In recent years, mechanical systems that use drive trains and fluid parts have become smaller and more precise due to high pressure and computerization. As a result, the clearance of parts used has become narrower and more sensitive to contaminated particles. Manufacturers of automobiles and construction machinery that mount these components are required to manage in the same cleanliness as the hydraulic components of aircraft. On the other hand, many hydraulic and lubrication devices are used in steel and automobile production lines, including power plants. As a matter of course, preventive cleanliness management is required to avoid mechanical blockage, damage, and wear of these equipment. To meet these high demands for cleanliness control, it is necessary to use a particle counter that shows the concentration level of contaminated particles within liquid. We have earned a high reputation in the market for supporting the technological utilization of particle counters as well as improved cleaning.
In highly contaminated lubrication systems, contaminated particles that enter the clearance induce wear, creating and increase another contaminant. In addition, the wear particles invade other component clearances and cause a chain of wear. As this chain of wear increases and the system looses its balance between the amount of particles and the amount of what filtration can hold, the life of the machine shortens. To extend the life of the lubrication system, oil cleanliness must always be maintained at a high level to prevent mechanical wear. Keeping oil clean requires the right knowledge of oil particle counter monitoring and contamination control. Intechno expertise in contamination control and lubrication control as well as cleanliness control.
Although in most cases for monitoring contamination in oil, samples are collected in bottles and analyzed with microscopes, there are problems such as validity of the sampling and the time and effort required. As a solution to this problem, the demand for online real-time monitoring technology increased and became a global standard. The demand is skyrocketing in two main areas. One is the process of manufacturing drivetrains and fluid components. The quality can be improved by constant inspection of the fluid inside the product. Another area is equipment maintenance for hydraulic and lubrication equipment. Monitoring hydraulic fluids and lubricating oils online can avoid downtime and improve production efficiency. As a pioneer of online real-time monitoring system, we provide technical support from installation to operation.